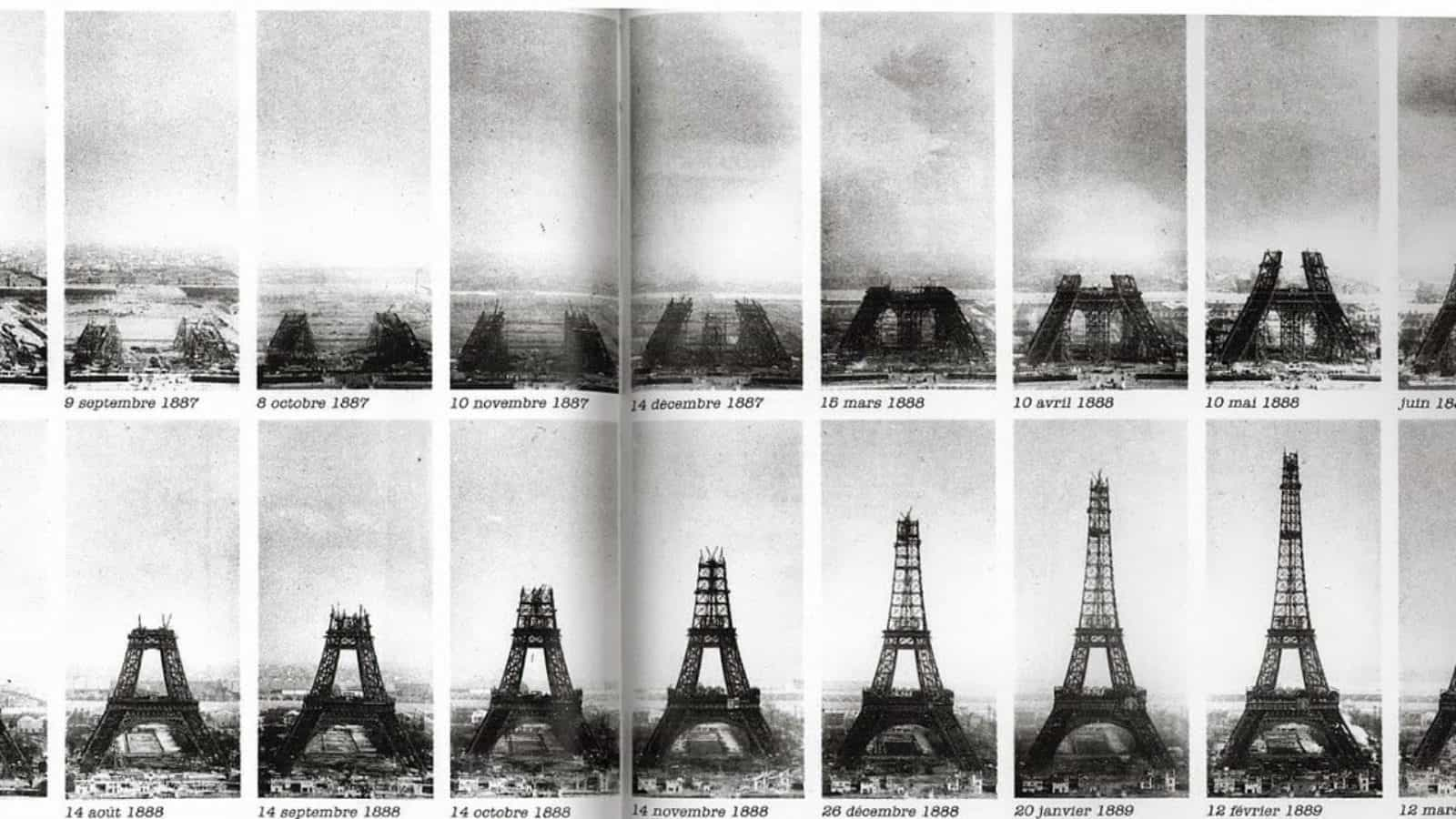
The construction industry is booming, and experts predict it will continue to be one of the fastest growing industries in 2020. And yet the sector suffers from low productivity — indeed, a gap between supply and demand. Companies are turning to new technologies to reinvent themselves, modernize their processes and boost output. In 2017 alone, more than $735 million, was invested in construction tech companies.
Through our Global Open Innovation Network that connects major corporations with the startups and SMEs they need to stay on the cutting edge of technological development, we gathered a panel of experts to better understand the massive changes happening now in the construction industry.
Here’s what we learned from:
- Jay Snyder (moderator), Technology Practice Leader at FMI
- Martin Rozmanith, Sales Director, AEC Industry at Dassault Systèmes
- Adrien Chaussinand, Head of Innovation and Partnerships at Winnovation
- Ian Howell, Executive in Residence at Building Ventures
Adrien Chaussinand opened the discussion and explained how French construction giant Bouygues, Winnovation’s parent company, is able to consistently innovate after 80 years in the industry. The group’s strategy includes intrapreneurship initiatives, open innovation, scouting teams and separate investment funds for each branch of the company. The group also takes risks by buying technologies or integrating new technologies as a client.
According to Ian Howell, population growth and global urbanization are the two main forces driving innovation in the construction sector. The problem remains that construction companies cannot keep, fueling the need for disruptive solutions. Ian illustrated this unbalance with an example from the United Kingdom: the government is forecasting the need for 5.3 million homes by 2040, which translates into one new home every five minutes for the next 22 years. The issue? Today it takes about 7 months to build a single-family house, according to the National Association of Home Builders. In other words, things need to change if construction output is to keep up with the needs of a growing and increasingly city-dwelling population.
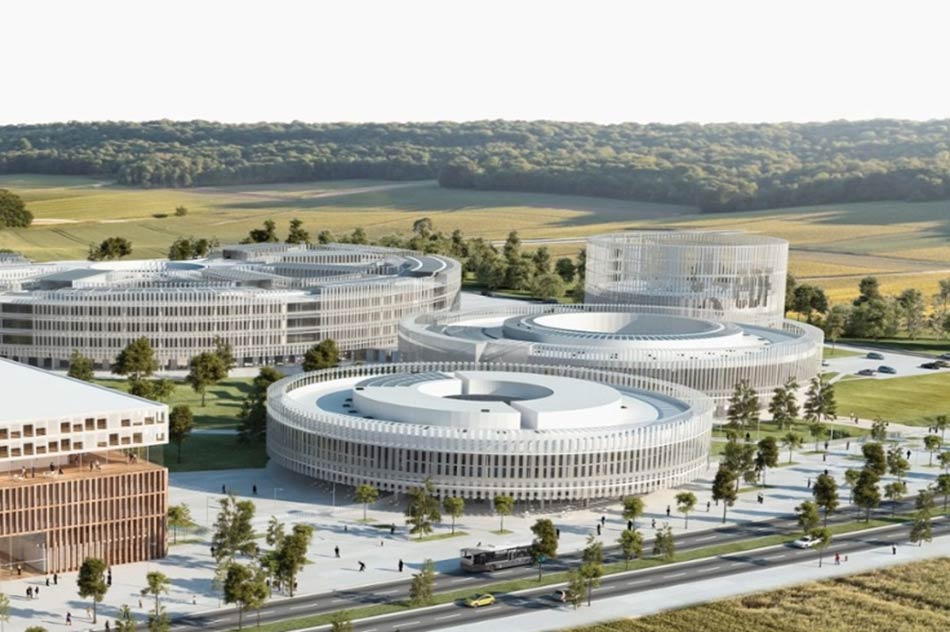
Our panel brought up the concept of Constructuring– the marriage of construction and manufacturing — as a way to increase supply to meet demand. By democratizing prefabrication and modular construction, companies can simultaneously avoid weather delays, cut costs, reduce waste and limit pollution — all while improving overall quality. Also, constructuring allows companies to train and deploy unskilled labor at a time when there is a huge shortage of skilled construction workers.
Martin Rozmanith recommended three ways to optimize constructuring:
- Use data to redesign the supply chain and minimize frictions
- Get rid of the subcontractor model to reduce costs, errors and delays
- Source globally instead of relying on regional suppliers and manufacturers
Adrien Chaussinand also insisted on the importance of data as a proven way to drive the accuracy of modular construction and increase transparency.
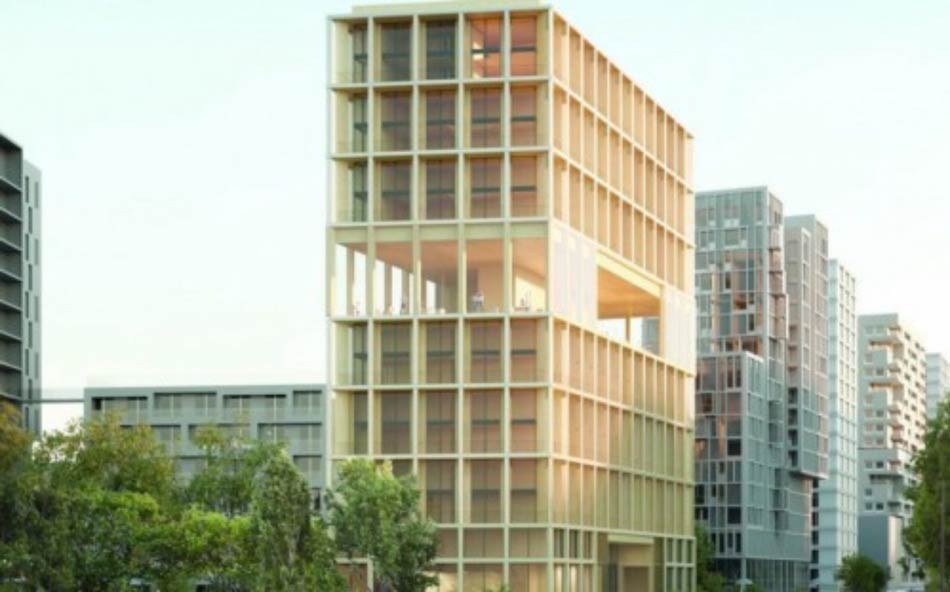
Ian Howell shared an example of an innovative company that successfully implemented modular construction, data management and supply chain optimization. In 19 days, Mini Skies City, a Chinese Construction company, built a 57-story skyscraper, at an average rate of three floors per day (check out their time-lapse video here).
Finally, the panel discussed sustainability issues and provided a set of recommendations: source more sustainable materials, improve expertise in the public sector for inspection and integrate the supply chain to have a better control over sustainability subjects.